立体的なデザインを細部まで表現
最新のエアロパーツ開発に迫る!!
クルマのカスタマイズに欠かせないエアロパーツ。
一般的には、発泡ウレタンやクレイ(粘土)で実物大の試作形を製作。
そこからマスター型(クレイから型どって作られた状態)を完成させて、製品を量産化するという工程だ。
いま、エアロパーツの開発で注目されているのが“3Dプリンター”を使用したもの。
小物ならば理解できるけど、どうやって大型のエアロパーツ生産に利用されているのだろうか。その開発現場に迫ってみた。
現場となったのは、KカーからセダンやSUVまで幅広い国産車だけでなく、近年ではインポートカーをも手がけるエアロパーツメーカー「エムズスピード」。
高級かつエレガントなデザイン性は高い評価を受けるが、その製作はパソコンを使って3D‐CADで設計し、3Dプリンターで出力するという最新のデジタル方式を採用している。
モデラーが実物大の試作品を製作するには相当の時間がかかるが、設計図に基づき3D-CADで具現化するだけ。3Dの立体画像なので四方からチェックでき、変更点があればパソコンで細部を修正。設計図ができ上がれば、そのデータを3Dプリンターで出力すればマスター型の元となる試作品が完成するわけだ。
また、モデラーが嫌がるような複雑なデザインにも対応。複雑なアールなどの造形を細部まで表現することも可能だという。というわけで、実際に工程を追ってみよう。
次ページで「現車をスキャン」>>>
01.現車をスキャンする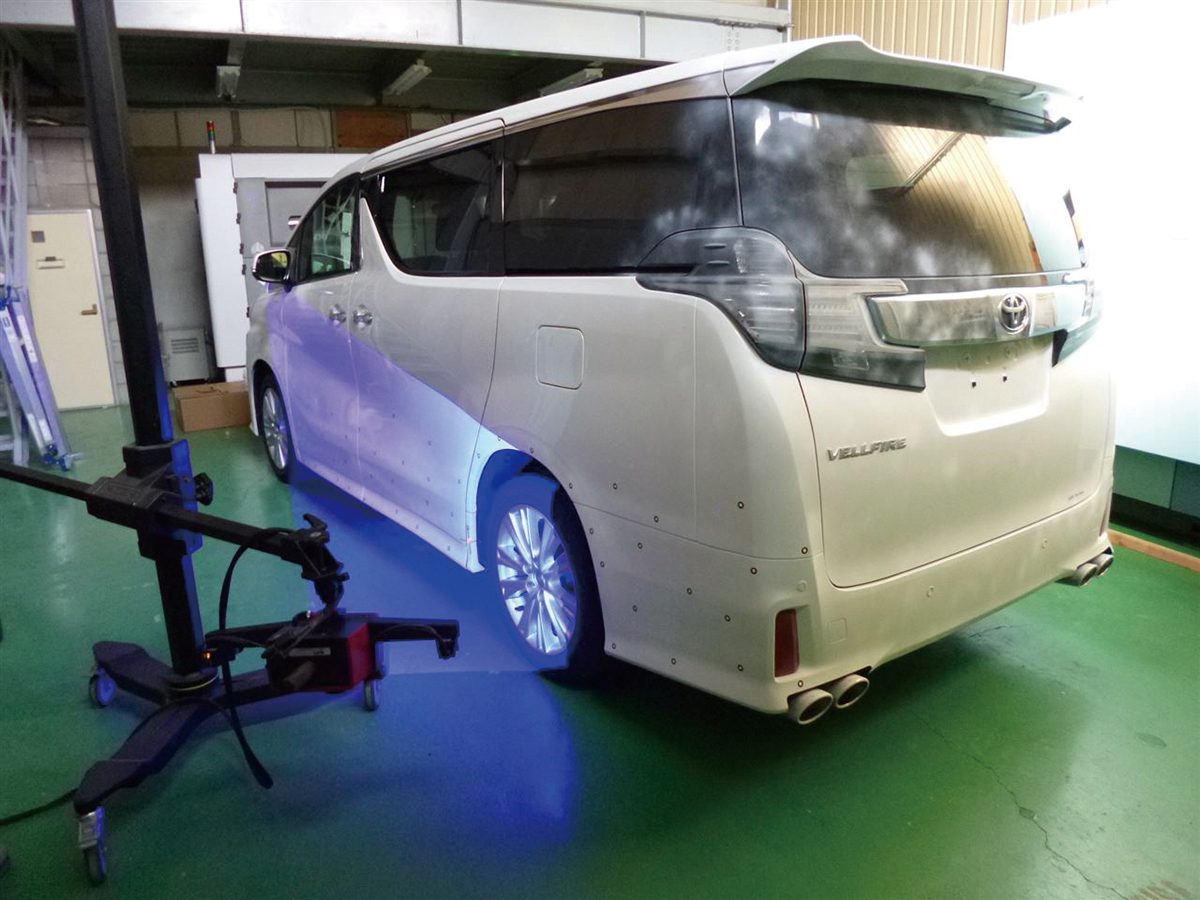
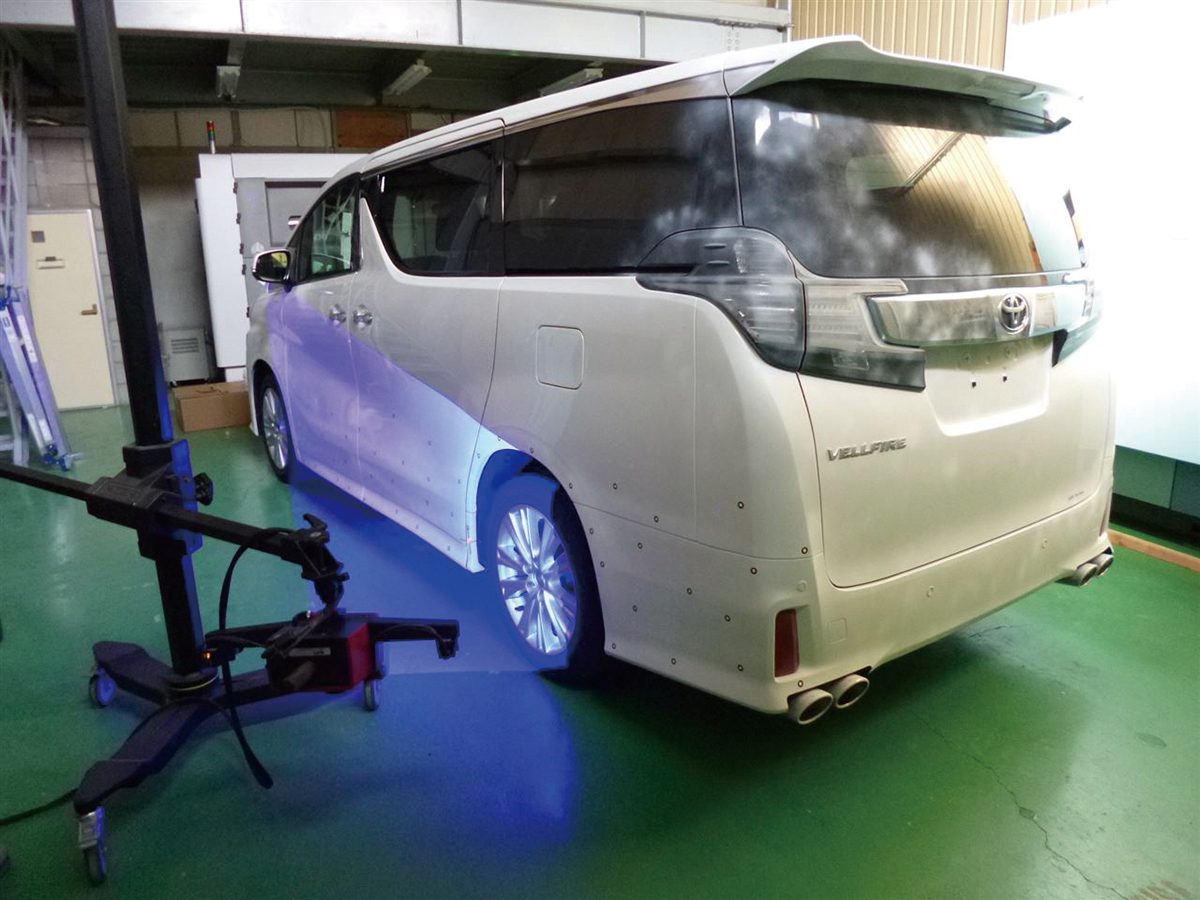
エアロパーツを製作するクルマの各パートを非接触スキャニングで計測。
非接触スキャニングは、表面の凹凸を計測することでボディの各サイズを1/100mm単位でデータ化することが可能のため、車体やバンパーとのフィッティングを高めることができる。
なお、計測が終了すれば現車の出番は終了だ。
02.イラストを元に3D-CADでデータ製作
2次元の設計図を見ながらスキャンした純正バンパーの上に3次元ラインを描いていく。画面上では折り紙を重ねていくようなイメージだ。
ちなみに「エムズスピード」が使用する3D-CADソフトは、自動車メーカーも採用しているキャティア製。複雑な曲面で構成されるエアロデザインも忠実に再現してくれる。
3Dプリンターで製作できるサイズは、50×50×70cm以内。
そのため、写真のトヨタ・50系プリウス用フロントバンパーでは12分割にデータ化する。
モデラーの職人技を必要とする、細かなデザインにも対応できる3D-CAD設計。
シミュレーションによる風洞実験も行なえるのだが、価格もハンパじゃないようだ。
次ページでいよいよ試作品エアロを「3Dプリンター」出力>>>
03.いよいよ3Dプリンターで出力
12分割されたフロントバンパーのデータを、ひとつずつ積み重ねるように配置してスイッチをON。
「エムズスピード」が導入しているのは、粉末焼結方式の3Dプリンターだ。
樹脂の元になる粉末にレーザーを当てて熱で固めていく方式で、レーザーが当たるのは0.1mmの粉末層。1cmを成型するのに約1時間かかるため、12分割したフロントバンパーでは60時間ほど待機することになる。
04.成型されたパーツを取り出す
3Dプリンターによる作業を終えると、製品を取り出すためのブレイクアウトステーションへと移動。
白い粉末を取り除いていくと、ナイロン樹脂製の12分割された各パートが出てくる。この時点で初めて実物大のパートが再現されるわけだ。
05.パーツをつなぎ合わせて一体化
写真は8分割となるプリウスのリヤバンパー。
ブレイクアウトステーションから取り出した各パートは、ボルトで締めながら接着。この完成形がクレイモデルと同じ型となり、マスター型→本製品が生産されるのだ。
「エムズスピード」では当初、3D-CADによる設計だけを先行させていたが、2年ほど前に3Dプリンターを導入したことで、完全デジタル化を図った。
こうやって発売されたばかりのニューモデルに素早く対応。完成度の高いエムズスピードのエアロパーツができるというわけだ。
M’z SPEEDのエアロラインアップはコチラ
取材協力:エムズスピード TEL06-6745-0200
http://www.mzspeed.co.jp/